中国铁合金网讯:
汽车结构件应用有望从小型件向大型件过渡
镁下游需求有望迎来爆发
2.1 节能减排驱动汽车轻量化进程 镁是未来最值得轻量化的材料
“节能减排”驱动轻量化进程:2016年中国汽车工程学会发布《节能与新能源汽车技术路线图》提出:至2020年,乘用车新车平均油耗5.0升/百公里,2025年4.0升/百公里,2030年3.2升/百公里。国外政府也对汽车能源消耗和污染排放制定了高压限制,2020年欧盟、日本汽车百公里耗油目标降至3.8L、4.9L。而轻量化是节能减排最有效的措施:车重每减少100g,燃油车百公里油耗可减少0.3-0.6L;车重每减少50%,CO2排放量能减少13%;整车质量降低10%,燃油效率可提高6-8%。因此“节能减排”号召将进一步推动轻量化进程。
新能源汽车对于轻量化需求更加迫切:根据2020年11月发布的《新能源汽车产业发展规划(2021—2035年)》,到2025年纯电动乘用车新车平均电耗降至12.0千瓦时/百公里,新能源汽车新车销售量达到汽车新车销售总量的20%左右。按照中国汽车工业协会公布的2019年全年汽车销量2577万辆估算,2025年我国新能源汽车年销量将超过500万辆。
新能源汽车除了没有发动机外,其他零部件与普通汽车并无本质差异,然而目前新能源汽车市场受制于续航里程与价格的平衡,电池数量及能量密度的提升短期内均较难实现,为追求降低电耗对轻量化材料的需求更加迫切。若新能源汽车每减少100Kg重量,续航里程可提升10-11%、电池成本减少20%、日常损耗成本减少20%,因此材料轻量化成为解决新能源汽车难题的关键路径。随着人们消费观念与环保意识的转变,未来新能源汽车快速发展将拉动轻材料产业迅速成长。
轻量化呼唤镁合金登场:汽车轻量化主要目标是轻质材料代替钢铁,最初是由铝合金对钢铁材料的替代,而随着镁合金压铸技术不断进步、良率逐渐提升,镁合金结构件对铝合金结构件的替代使得汽车轻量化更进一步。镁合金密度之低仅次于昂贵的碳纤维材料,强度高于铝合金和钢,比刚度远超工程塑料,具有良好的铸造性和抗震减噪能力,且能100%回收利用,诸多优势使得镁合金成为汽车轻量化最重要的材料之一。
材料间成本差距逐步缩小 镁合金应用迎来重要机遇:2016-2017年的供给侧改革有效出清钢铁过剩产能,使得钢价涨幅远超镁、铝,原材料成本差距大幅改善,镁铝之间的成本也得到有效缩减。随着镁产业日渐成熟,未来在汽车轻量化领域的应用将更加广阔。
我国单车用镁增量空间大:汽车是镁合金最重要的下游,然而我国千人汽车保有量较低,产品轻量化也属于落后水平,根据2015年数据,相比美国平均每辆车消耗镁合金3.8kg、日本9.3kg、欧洲14 kg以上,我国单车耗镁仅1.5kg,国家轻量化发展目标指出:2020年,我国单车镁合金用量须提升至15kg,2030年我国单车镁合金用量须提升至45kg。目前来看,在镁合金轮毂等相对较大的部件普及之前,2020年单车镁合金目标在部分车型上或能够实现,平均单车镁合金用量达到15kg仍存难度,但未来随着我国汽车保有量的不断突破,轻量化水平跟上国际步伐,单车用镁增量空间不容小觑。
2.2 汽车产业链龙头企业纷纷布局镁行业 看好镁在汽车轻量化广阔空间
宝钢金属入股云海金属,布局镁合金轻量化领域:宝钢金属是宝武集团多元业务旗舰子公司之一,业务涵盖金属制品、工业气体、汽车贸易与服务等。母公司宝武集团是全球领先的特大型钢铁联合企业,作为国内唯一具有汽车板全品种的钢铁供应商,汽车板产量稳居国内第一、世界前三,冷轧板等产品市占率超过60%,宝钢在全球率先具备第一二三代超高强钢研发和批量供应能力,已跻身国际知名汽车制造供应商行列。2018年12月、2020年8月宝钢金属两次增持云海金属股份,目前共持有14%股份,是公司的第二大股东。
根据云海金属11月24日公告,云海金属、宝钢金属、安徽省池州市青阳县人民政府签订高性能镁基轻合金及深加工项目合作框架,拟共同投建年产30万吨高性能镁基轻合金及深加工项目,涉及建设年产 30 万吨高性能镁基轻合金、15 万吨镁合金深加工产品等。项目若全面实施,将进一步保证镁合金产品的供应,推动镁行业健康发展,提高公司在镁合金及深加工领域的市场占有率,云海金属与宝钢金属在轻量化领域的协同效应也将进一步提升。
电池巨头携手三祥新材,布局镁铝合金领域:2020年8月26日三祥新材发布,拟与宁德时代新能源科技股份有限公司、江苏万顺机电集团有限公司、中山市隽达股权投资管理企业、中山银泰股权投资管理企业共同投资镁铝合金项目,实施主体暂定名为宁德文达镁铝科技有限公司,注册资本为30,000万元,宁德时代、万顺集团、三祥新材、隽达投资、银泰投资按25%;17%;35%;9%;14%的比例共同投资。项目合作的产品为镁铝合金,总投资额3亿元。根据我们调研,未来宁德文达镁铝有望在镁合金电池包领域实现产业化,推动镁合金结构件在新能源汽车轻量化应用领域再下一城。
宁德时代是新能源汽车动力电池龙头企业,2019年在全球动力电池领域位居首位,市占率达到27.9%。在国内动力电池领域,宁德时代也具有统治级地位,2019年公司国内动力电池市占率达50.6%,三元电池及磷酸铁锂电池市占率均超过50%。本次宁德时代携手三祥新材布局镁合金领域,彰显新能源汽车产业链龙头对于汽车轻量化未来前景的看好以及对于镁合金应用前景的信心,同时也有望加快镁合金结构件在市场推广的步伐。
2.3 镁合金汽车结构件应用有望从小型件向大型件过渡 轮毂等重磅需求即将迎来爆发
轻量化有望实现由小型化向大型化发展:目前可用的镁合金汽车零部件有转向支架、方向盘骨架、气囊支架、泵壳、泵盖、座椅支架,仪表盘支架、车门内框、车盖、轮毂等。受限于锻造加工难度以及成本问题,部分大型结构件仅在高端赛车上有所应用,较为普及的镁合金零部件主要为转向支架、仪表盘横梁、方向盘支架等小型结构件。近年来随着锻造技术进步,大型结构件良率逐渐提升,锻造加工成本下降使得价格逐渐具有竞争力,部分大型结构件已经具备普及的可能。
海外通用、奔驰等知名车企逐渐接受镁合金轮毂的应用:通用汽车旗下凯迪拉克近期宣布将锻旋(锻造+旋压)镁合金轮毂将作为可选配置,将随着2022款CT4-V BLACKWING和CT5-V BLACKWING车型于2021年夏季在北美市场上市。应用该款锻旋镁轮替代相同尺寸的锻造铝轮可以获得大于8公斤的簧下质量的减轻,从而带来更短的加速时间以及更强的操纵性,并且能够增强燃油经济性。除通用汽车以外,2019年底德国奔驰设计公司与国内镁合金轮毂生产商德威科技签署3年5亿元镁合金轮毂采购协议,奔驰、宝马、保时捷等德系高端汽车后续也有望将镁合金轮毂作为可选配置。
在悲观预测情况下,假设2025年燃油车镁轮毂渗透率达到6%,新能源汽车中渗透率达到10%,则轮毂领域镁合金用量将增加11.41万吨。
在乐观预测情况下,假设2025年燃油车镁轮毂渗透率达到13%,新能源汽车中渗透率达到17%,则轮毂领域镁合金用量将增加23.82万吨。
2.3 镁电池支架及电池包外壳极具推广前景 放量后有望再度拉动镁合金需求
电池包是新能源汽车核心能量源,为整车提供驱动电能,纯电汽车的电池包重量可达数百公斤。电池包组成主要包括电芯、模块、电气系统、热管理系统、壳体和BMS,其中电池壳体是新能源汽车动力电池的承载件,一般是安装在车体下部,主要用于保护锂电池在受到外界碰撞、挤压时不会损坏。传统车用电池箱体采用钢板、铝合金等材料铸造,然后对表面进行喷涂处理。随着汽车节能环保要求不断提升,目前部分企业开始尝试使用镁合金材料实现电池包壳体、电池支架的轻量化。
根据我们调研的情况,部分镁加工企业已开始向车企推广镁合金电池支架,该结构件使用铝合金材料时重量在14-15公斤,现在使用镁合金材料只需要7-8公斤,减重效果达到40-50%。
在悲观预测情况下,到2025年电动车镁合金电池支架领域将增加镁合金需求量1.30万吨;在乐观预测情况下,将增加镁合金需求量2.85万吨。
目前三祥新材与宁德时代等企业合作已研发成功镁合金电池包外壳,只待最后一步建立生产线实现产业化。以特斯拉MODEL S为例,其电池包外壳采用铝合金材料,重量达125公斤。采用镁合金材料制成的同样尺寸电池包外壳只需要60-70公斤,减重效果达50%,可以有效降低汽车重量,提升汽车续航能力以及操作体验。根据调研反馈的信息,镁合金外壳不仅安全可靠性优良,而且规模化生产以后,镁合金电池包外壳成本比铝合金外壳更低,未来应用前景广阔。
考虑到不同尺寸电池包外壳重量差异较大,假设镁合金电池包外壳平均重量为40公斤,在悲观预测情况下,到2025年电动车镁合金电池包外壳领域将增加镁合金需求量3.48万吨;在乐观预测情况下,将增加镁合金需求量8.69万吨。
链接阅读:
内容来源:长城有色
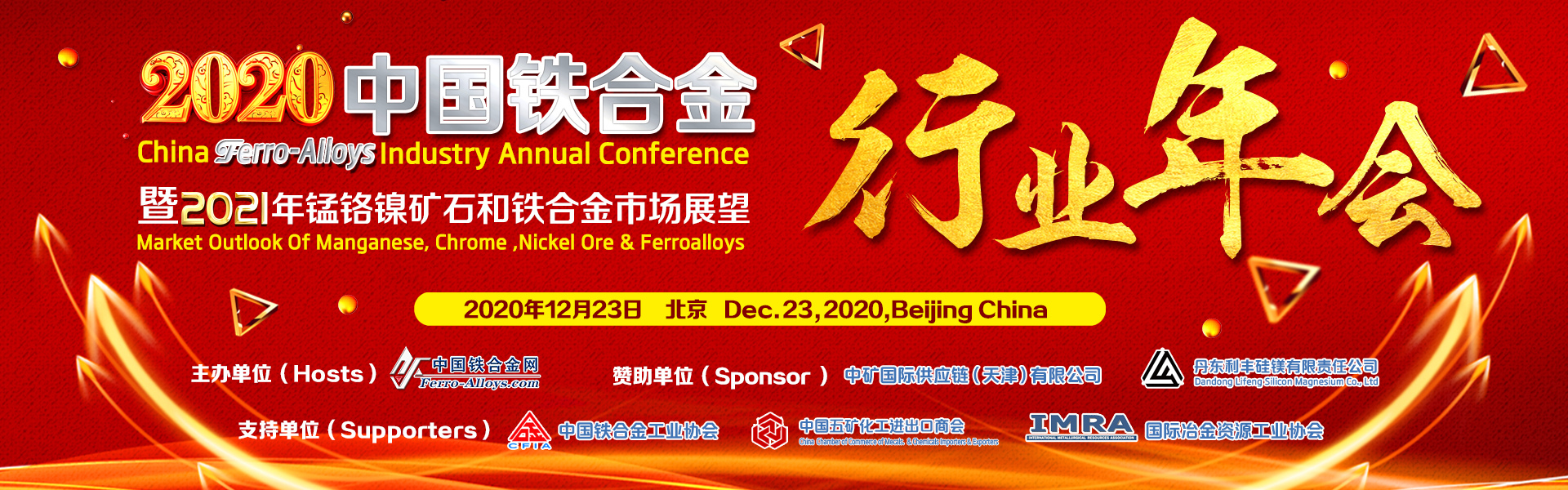
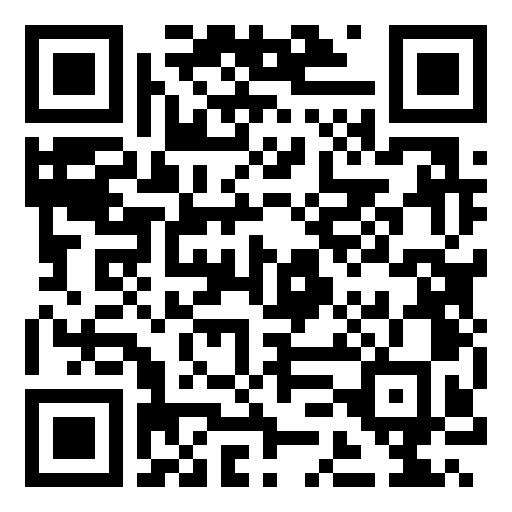
- [责任编辑:kangmingfei]
评论内容