中国铁合金网讯:
在铸件生产的过程中,错综复杂的内外因素影响着铸件的质量,其中缩松是较常见的铸件缺陷。避免缩松缺陷的途径有很多,本文讨论其中的一个重要影响因素:碳当量、硅含量和镁含量的控制。其它影响因素我们将在后续的推送中继续分享。
首先,采用多大的碳当量?
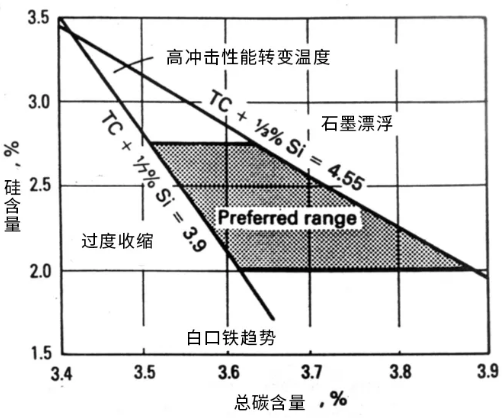
图1
图1展示了为避免缺陷如何选择合理的碳当量的原则。我们不仅要避免缩松缺陷,也需要避免石墨漂浮缺陷的产生。图中建议总的碳含量加上三分之一的硅含量不应该超过4.55%。
这个图表是针对壁厚在13mm到38mm之间的一般壁厚的铸件。对于壁厚非常薄的铸件例如排气歧管,碳当量可能更高。对于壁厚较厚的铸件,碳当量应较低,以避免石墨漂浮和产生缩松缺陷。
在凝固过程中碳从金属液中析出,产生石墨化膨胀。当铁水以共晶方式凝固时,碳含量最高时缩松最小,此时的碳含量刚刚低于发生初始石墨析出和石墨球开始上浮时的碳含量。
采用最高的碳含量且避免石墨球漂浮

图2
图2是由英国铸铁研究协会为美国铸协一项研究项目制作。该表展示了不同形状壁厚的铸件在避免石墨漂浮时不同的硅含量对应的最大碳含量。这也是缩松趋势最小化时碳含量所能达到的最大值,其中也包含了不同浇注温度下的数值修正。
假设凝固时持续遵循共晶过程,一般来说随着碳含量的增加缩松减少。共晶凝固时,奥氏体壳内的石墨析出与生长同时进行。如果碳含量过高,凝固过程开始时先发生初生石墨析出,由此产生的大量膨胀作用在凝固早期就被消耗掉。这是由石墨快速析出并悬浮在液态金属液中引起的。这可能导致在凝固后期,即铁水被隔离成孤立点的情况下,石墨化膨胀不足。
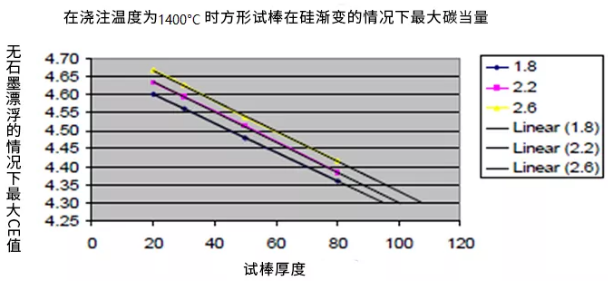
图3
图表3中的数据是从前图中方形试棒中获得的。有三条曲线展示了三个不同硅含量的情况,这些曲线一直延伸到碳当量为4.3%的横线。这表明超过一定厚度时碳当量必须处在或低于共晶点。所有较厚的截面的碳当量都必须等于或小于4.3%,以避免初生石墨的析出、石墨漂浮以及产生较高的缩松趋势。对于方形试棒,随着硅含量从1.8%变化到2.6%,该转变点从厚度为95mm变化到108mm。
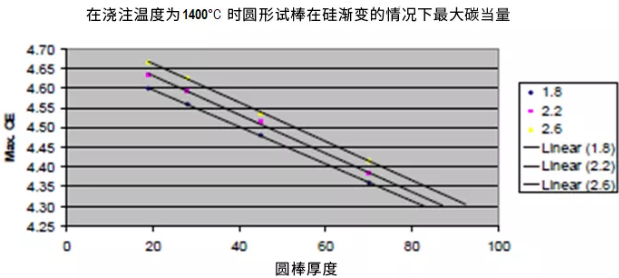
图4
图4中显示了转变为圆棒直径的等效数据。当圆棒截面在含硅量为1.8%时达到83mm,其碳当量应在4.3%或者更小。
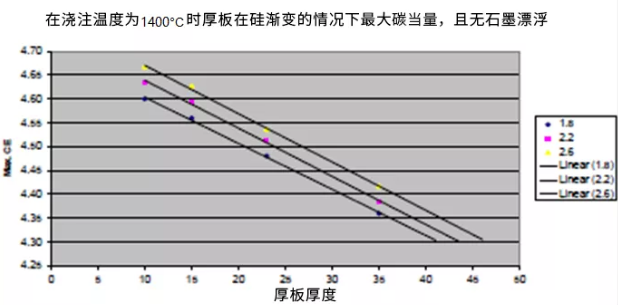
图5
在图5中方形试棒的数据被转化为等效厚度的板型试块。对于含硅量为1.8%的球铁,当截面厚度达到或超过42mm时,碳当量应等于或低于4.3%。
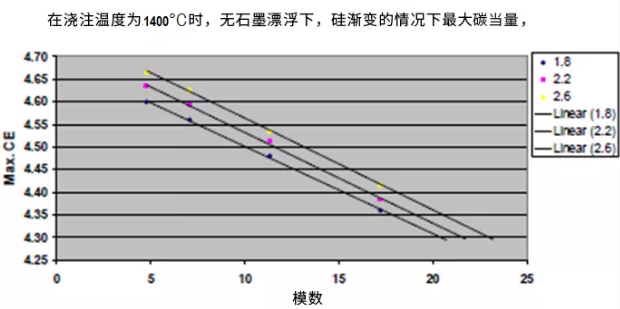
图6
图6中的数据是方形试块的数据转化为等效模数。模数是指铸件的体积与面积的比率。数据线延伸至碳当量等于4.3%的水平线,指出碳当量必须等于或低于4.3%,以避免石墨漂浮的模数。
硅含量在1.8%时,模数是21mm。
硅含量在2.2%时,模数是22mm。
调整碳析出产生膨胀的时间
在凝固开始时,碳作为石墨球析出从而保证碳不会在边缘激冷时产生碳化物。同时应避免形成过多的早期石墨析出相,否则会导致在最后凝固时只有少量的石墨析出,这时浇注系统和冒口已无法提供金属液来补偿收缩。可见了解影响凝固各阶段中石墨析出量的铸造变量十分重要。
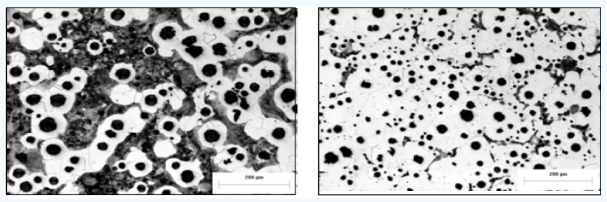
图7
较高的硅含量可以直接带来较多的石墨球数、铁素体量和早期石墨析出相。为了减小缩松,建议在碳当量一定时采用最大的碳含量和最小的硅含量。碳提供膨胀作用,同时太多的硅含量能引起过度的初始膨胀作用以及最终铁水凝固时较少膨胀作用。
硅含量的水平应满足避免产生碳化物和提高铁素体以得到合格机械性能的要求,同时要避免过量。具有相似的结构特点、大小一致的过量的石墨球数会导致缩松的情况。在这种情况下所有的石墨球都是在早期凝固时同一时间形成的。这样的金相结构很好看,但是不利于消除缩松。图7展示了石墨球数是怎样随着硅含量而变化的。
其他的影响因素也可能产生较多尺寸一致的石墨球,如过多的孕育剂加入量或者使用铋来提高石墨球数。但是在石墨球的尺寸分布范围较大时,石墨球数较多对于减少缩松是有利的。这意味着石墨是在凝固开始到结束过程中稳定析出的,而不是在凝固初期快速形成的。
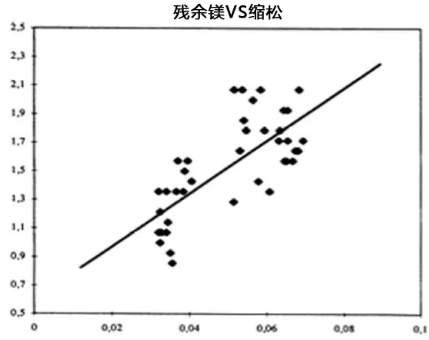
图8
镁含量是影响缩松的另一个因素,严格控制镁含量可以减小缩松倾向。图8显示了随着最终镁含量的增长,缩松倾向增加。充足的镁含量是获得较好石墨球所必需的,但是要避免过量。过量的镁会引起一些其它类铸件缺陷,如夹渣、白口、钉状石墨等等。
内容来源:埃肯铸造
中国铁合金网版权所有,未经许可,任何单位及个人均不得擅自拷贝或转载,否则视为侵权,本网站将依法追究其法律责任,特此郑重声明!
- [责任编辑:kangmingfei]
评论内容