概述~操作制度
为使高炉生产达到高效、优质、低耗、长寿的目的,须根据高炉使用的原料、燃料条件,设备状况以及冶炼的铁种,制定基本操作制度。它包括热制度、造渣制度、送风制度和装料制度。各项基本操作制度之间彼此有内在联系,制定基本操作制度时要综合全面考虑。例如装料制度可以影响炉料和煤气流分布,送风制度也影响煤气流分布,必须将二者结合起来考虑。又如造渣制度与热制度也须综合考虑:炉渣碱度定得低时生铁含硅量不能定得太低,否则,生铁含硫量太高,影响生铁质量;反之,当炉渣碱度较高或渣中MgO较高时,生铁含硅量则可定得低些。送风制度与热制度也有联系:炉温高时(例如冶炼铸造生铁或锰铁)冶炼强度要低些;炉温低时则冶炼强度应高些。
1.热制度
根据冶炼铁种、原料、燃料条件和炉容大小而确定的炉缸应具有的温度水平称为高炉热制度。一般以铁水和炉渣的温度为代表。由于原料质量、炉容大小、冶炼铁种和操作制度不同,各个高炉的铁水和渣水的温度水平是不同的。铁水温度多在1400~1530℃之间,炉渣温度约比铁水温度高50~100℃。在一定原料和冶炼条件下,生铁含硅量(〔Si〕%)与炉温成正比关系。炉温高则生铁含硅量高;反之,则低。以铁水和炉渣温度代表的炉温称“物理温度”,以〔Si〕%代表的炉温称“化学温度”。由于测量铁水和炉渣的温度比较麻烦,而生铁含硅量又是一个重要控制成分,所以高炉操作者习惯以生铁含硅量作为衡量炉温的标志。于是热制度实际上就成了高炉操作者对根据原料条件和冶炼铁种而选定的生铁含硅水平的控制。冶炼炼钢生铁时〔Si〕%较低,炉温较低,确定热制度时应充分考虑炉缸的“物理温度”。当原料熟料比高,还原性好时,炉缸“物高 gao理温度”高,〔Si〕%可确定在较低水平,同理,当炉渣碱度较高时〔Si〕%也应选择低些;反之,〔Si〕%则选择在较高的范围。炉容太小时〔Si〕%应选择在较高的范围。当原料含TiO2较高时,〔Si〕%应控制得尽可能低些。除〔Si〕外,还要控制〔Ti〕%。〔Ti〕%也是随炉温高低而升降的,〔Ti〕不宜超过0.2%。否则由于钛还原生成的TiC、TiN、Ti(N,C)过多,导致铁水、渣水黏稠而使高炉不能正常生产。冶炼铸造生铁时,焦比高,炉缸热量充足,确定〔Si〕%的范围只需满足冶炼的牌号即可。冶炼锰铁时,焦比更高,炉温也更高。确定热制度时,主要是确定〔Mn〕%的水平,〔Mn〕%必须达到冶炼牌号的要求。
在现代高炉生产中,更以通过计算机运算和显示的风口前理论燃烧温度t理和燃烧带的炉温指数tc及时判断炉缸热状态。因为高炉的高温热量来自风口前燃料的燃烧,t理说明能提供多高温度,tc则说明燃烧带形成的高温煤气能通过传热加热炉料或形成的产品达到多高温度,特别是在高炉喷吹燃料之后,这一点尤为重要。t理一般应在2050~2300℃,而tc则应达到0.75t理。
2.造渣制度
根据原料、燃料条件和冶炼铁种来确定炉渣的成分和碱度,称为高炉造渣制度。据此获得熔化性、流动性、稳定性均好,脱硫和排碱能力均强的高炉炉渣。炉渣碱度(CaO/SiO2或(CaO+MgO)/SiO2)是造渣制度的一个重要参数。碱度高,脱硫效率高;反之,则脱硫效率低。碱度的选择主要根据原料、燃料含硫量的高低。但碱度过高的炉渣熔点高,流动性差,稳定性不好,不利于炉况顺行,且多消耗焦炭,因此,在保证生铁含硫量合乎要求的前提下应选择较低的炉渣碱度。冶炼炼钢生铁时的碱度(CaO/SiO2)多在1.0~1.25之间;冶炼铸造生铁时;为避免炉缸堆积和有利于硅还原,碱度应较前者低一些。冶炼含碱金属高的原料时,为利于炉渣排碱,宜选用较低的碱度。冶炼锰铁时,为提高锰的收得率,碱度要高些,CaO/SiO2达到1.50左右。炉渣成分中的MgO一般控制在6%~12%,这有利于改善炉渣流动性和脱硫,有利于获得炼钢炉所需要的低硅低硫铁,也有利于炉渣排碱。Al2O3不宜超过15%,否则炉渣流动性差。
3.送风制度
根据炉容大小、设备状况、原料、燃料条件、风口喷吹状况和冶炼铁种确定鼓风数量、压力、温度、湿度、富氧率、风口风速(或鼓风动能)、风口前火焰温度等参数。
(1)风量
单位时间进入高炉的风在标准状态下的体积(m3/min或m3/h)。在相同条件下,风量越大,产量越高。高炉风量首先取决于高炉容积,一般是每立方米炉容2.0~2.2m/min。由于风量的测定常因漏风和仪表本身误差而失准,而风量又与焦炭和喷吹燃料的消耗量成正比,故高炉操作人员多习惯于以冶炼强度来估量风量。又因在同一条件下,高炉上料批数与风量成正比,故高炉操作者实际上是按上料批数来控制风量的。冶炼强度取决于原料、燃料质量和冶炼的铁种,一般在0.9~1.2t/(m·d)之间。原料、燃料质量好时取上限;反之,取下限。冶炼铸造生铁时的冶炼强度应比冶炼炼钢生铁时的低,冶炼锰铁时又比冶炼铸造生铁时的低。这是因为炉温越高,炉内煤气实际体积越大,穿过料柱越困难。当高炉需要限产时,冶炼强度和风量根据额定生铁产量来确定。鼓入高炉的风量和每小时上料的批数(炉内下料速度)应力求稳定。风量波动会影响料速和炉温波动,进一步会引起风压波动和炉况不稳。为此,高炉风量选定在某一适当水平后不宜随意增减。只有在炉凉、下料不顺或设备故障需要减风处理时才减风。减风后一旦条件允许恢复风量时,应及时逐步恢复。
(2)风速
鼓风在风口出口处的速度,通常以m/s为单位。风速对高炉下部的煤气流分布有重要影响。风速高,穿透力强,有利于延长风口回旋区,增加中心煤气流,提高中心温度。但风速并非越高越好,它根据不同条件有一个合适的范围。风速过小,容易导致炉缸中心堆积;风速过大又容易形成边沿堆积(见炉缸堆积)。风速有标准风速和实际风速之分:前者按标准状态下的风量计算,后者按高炉实际风温、风压下的风量来计算。高炉的标准风速多在80~200m/s之间。高炉越大,风口越多或越短,高炉的高径比越小,冶炼强度越低,富氧率越高,喷吹燃料越少,风速越接近上限;反之,则靠近下限。风速选择恰当,炉缸活跃,炉况稳定、顺行。故高炉操作者在确定风量以后,都要根据具体条件精心选取风速,并据此确定风口直径。有的高炉工作者用鼓风动能来衡量鼓风在风口前的穿透能力。鼓风动能对回旋区的影响比风速更切合实际一些,但计算更复杂。二者均通用。
(3)风温
高炉鼓风的温度。风温越高,鼓风带入炉内的热量越多,高炉的燃料比越低。因此,通常都将风温用到高炉可能接受的最高水平。高炉接受风温的程度主要决定于冶炼条件。原料、燃料质量越好,喷吹燃料越多,鼓风湿度越高,炉况越稳定、顺行,高炉能接受的风温越高。中国高炉风温多在900~1250℃之间;工业发达国家的高炉风温多在1150~1350℃之间。增减风温是调节炉况的重要手段,提高风温可以使炉温升高,降低风温可以使炉温降低。但先进的高炉多把风温稳定在最高水平,而用调整燃料喷吹量或鼓风湿度的办法来调节炉况。只有在非常必要时才降低风温。这样可以获得较低的燃料比。
(4)鼓风湿度
鼓风中的水蒸气含量。多以g/m3为单位。自然鼓风的湿度随大气湿度而变化,而鼓风湿度波动对料速和炉温都有影响,故不能任鼓风湿度自然波动。通常采用两种办法:通过脱湿鼓风将鼓风湿度控制在最低水平;或通过加湿鼓风将鼓风湿度控制在某一适当水平。喷吹燃料多时宜采用脱湿鼓风;不喷吹燃料或喷吹量少时宜采用加湿鼓风。采用加湿鼓风时变更鼓风湿度可以作为调节炉况的一个手段。
(5)理论燃烧温度
风口前焦炭和喷吹燃料燃烧时的最高火焰温度。此温度难于直接测定,多由理论计算得出,故称理论燃烧温度。理论燃烧温度有一个合适的范围,约在2000~2350℃之间。过低,炉缸温度低,容易导致炉缸工作失常;过高则生成SiO多,容易引起炉况不稳。原料、燃料质量好,渣量少,焦比低,炉况稳定时可偏上限控制;反之,偏下限控制。现代高炉多采用综合鼓风,影响理论燃烧温度的因素随之增多。理论燃烧温度与风温和富氧率成正变关系,与喷吹燃料数量和鼓风湿度成反变关系。几个因素要合理配合,以使理论燃烧温度保持在合理范围。为降低高炉燃料比,通常将风温保持在最高水平,将湿度控制在最低水平,而将喷吹燃料量和富氧率作为调整因素。
(6)风压
鼓风进入高炉前的压力。风压与炉顶压力、炉容和料柱透气性有关。炉容为1000~5000m3的现代高炉的炉顶压力多在0.1~0.25MPa之间,风压多在0.2~0.45MPa之间。风压等于炉内料柱阻力与炉顶压力之和。高炉操作人员先根据设备状况确定炉顶压力。炉顶压力越高越有利于高炉生产(见高压操作)。炉顶压力是自动调节的,其数值相对稳定,因此风压的水平及其变化可以反映炉内料柱阻力的水平和变化。它是高炉操作人员判断炉况的一个重要指标。风压越稳定,炉况越顺行。
4.装料制度
根据装料设备的类型、炉容大小和原料、燃料条件及配比确定批重、料线、装入顺序、布料器旋转角度和无钟炉顶旋转溜槽的工作程序:多环布料、螺旋布料或单环布料、料流调节阀开度,炉喉导料板的工作程序等。制订装料制度的目的是使炉料在炉内分布合理。合理的炉料分布结合适宜的风速可以得到合理的煤气分布,这是高炉稳定运行的基础。炉料分布合理的标志是:焦炭层和矿石层的厚度适当;环向分布均匀;径向分布:炉子中心矿焦比最低,由中心到边沿矿焦比逐渐升高,到靠近边沿处矿焦比又略有下降。焦层和矿层的厚度由批重决定,根据经验焦炭批重(t)约等于0.03dt3(dt为炉喉直径,m)或焦层厚度在炉喉为450~650mm。焦炭批重确定之后可根据焦比算出矿石批重。炉料的环向均匀分布靠旋转布料器或无钟炉顶的旋转溜槽的正确工作来实现;合理的径向分布靠调节料线、装入顺序和炉喉导料板的档位或无钟炉顶旋转溜槽的倾角来实现。
炉料和煤气流在炉内的分布状况是难以直接观察的,通常是根据煤气的温度和成分的分布情况来判断。在同一平面上,如果同环各点的煤气温度接近,说明炉料和煤气的环向分布均匀;反之,则不均匀。径向炉料和煤气的分布状况一般是根据沿炉喉半径各点的煤气成分(CO2%或CO2/(CO2+CO))分布曲线或温度分布曲线来判断的。
CO2%或CO2/(CO2+CO)%高处,料层的矿焦比高,煤气流弱;反之,则矿焦比低、煤气流强。煤气温度高处,料层的矿焦比低、煤气流强;反之则矿焦比高,煤气流弱。正常的煤气分布曲线大体呈双峰的M形或喇叭花型;正常的温度分布曲线与之相反,大体呈双谷的W形或倒喇叭花型。煤气流分布形态确定之后,可以运用批重、料线、装入顺序的布料特性和旋转布料器、炉喉导料板或无钟炉顶旋转溜槽的布料功能来获得所需要的炉料分布和煤气流分布(见高炉布料)。炉况的判断和调节。
高炉运行良好时,下料平稳、料速符合规定而且均匀,煤气流分布正常,风量、风压及各层静压力曲线平稳,炉顶压力曲线不出现向上尖峰,炉体各层温度曲线平稳,同一水平面上各方位温度接近,各风口温度均匀、活跃,风口、渣口极少烧坏,铁水质量好,铁水、渣水流动性良好、温度高而且均匀,高炉利用系数高、燃料比低。这种运行正常、良好的炉况即为炉况顺行。在实际生产中,由于原料、燃料质量的变化和称量的波动,设备运转的不稳定性以及鼓风参数的波动等,常常引起高炉炉况发生变化。这种变化如不能及时发现和调节,就会导致炉况失常,甚至造成高炉故障或发生事故,因此需经常对炉况进行监视和控制。监控的主要项目是炉温、炉料和煤气流的运动状况,炉渣碱度和炉衬侵蚀情况。
内容来源:高炉炼铁人
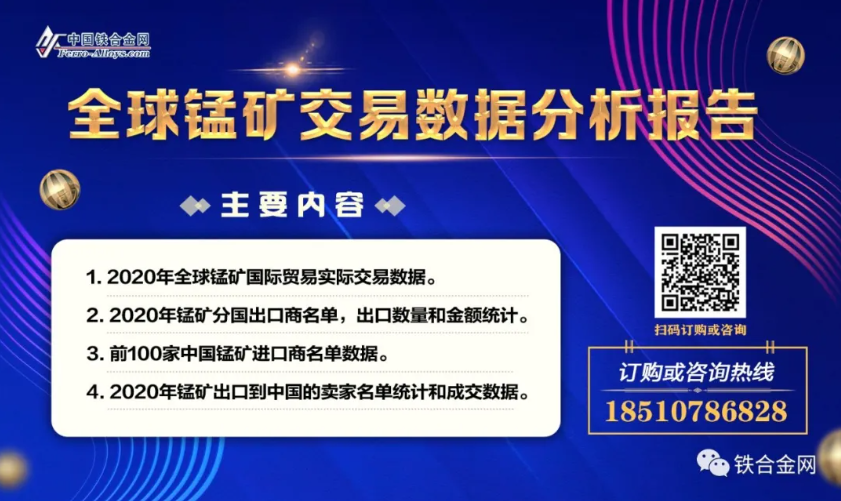
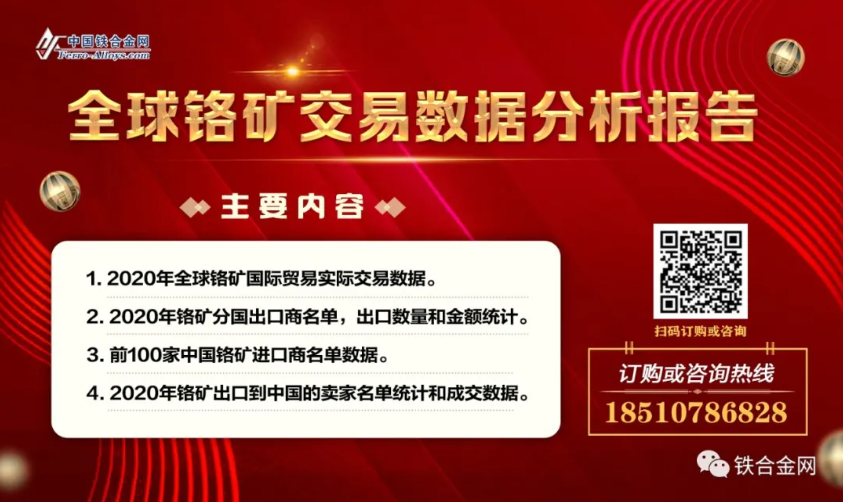
- [责任编辑:kangmingfei]
评论内容